Digital Twins in Industry 4.0: Revolutionizing Manufacturing
Understanding Digital Twins in Industry 4.0
The concept of digital twins is gaining momentum in the realm of Industry 4.0, offering transformative solutions for complex manufacturing processes. A digital twin is essentially a virtual replica of a physical asset, process, or system that enables real-time data analysis and monitoring. This technology fosters enhanced decision-making and process optimization, streamlining operations across the manufacturing landscape.
As manufacturers continue to seek greater efficiencies and innovations, digital twins stand out as a vital tool. By utilizing advanced analytics and machine learning algorithms, businesses can simulate scenarios, predict outcomes, and identify potential issues before they occur. This proactive approach significantly reduces downtime and enhances productivity.

The Role of Digital Twins in Manufacturing
Digital twins play a crucial role in revolutionizing the manufacturing sector by fostering a more connected and informed environment. These virtual models facilitate seamless integration across various stages of production, improving both product quality and delivery times. By connecting the physical and digital worlds, manufacturers can achieve a more synchronized and responsive production line.
One of the primary advantages of digital twins is their ability to provide a comprehensive overview of the manufacturing process. This holistic view allows companies to optimize resource allocation, streamline supply chains, and enhance collaboration across different departments. As a result, businesses can achieve significant cost savings while boosting overall efficiency.
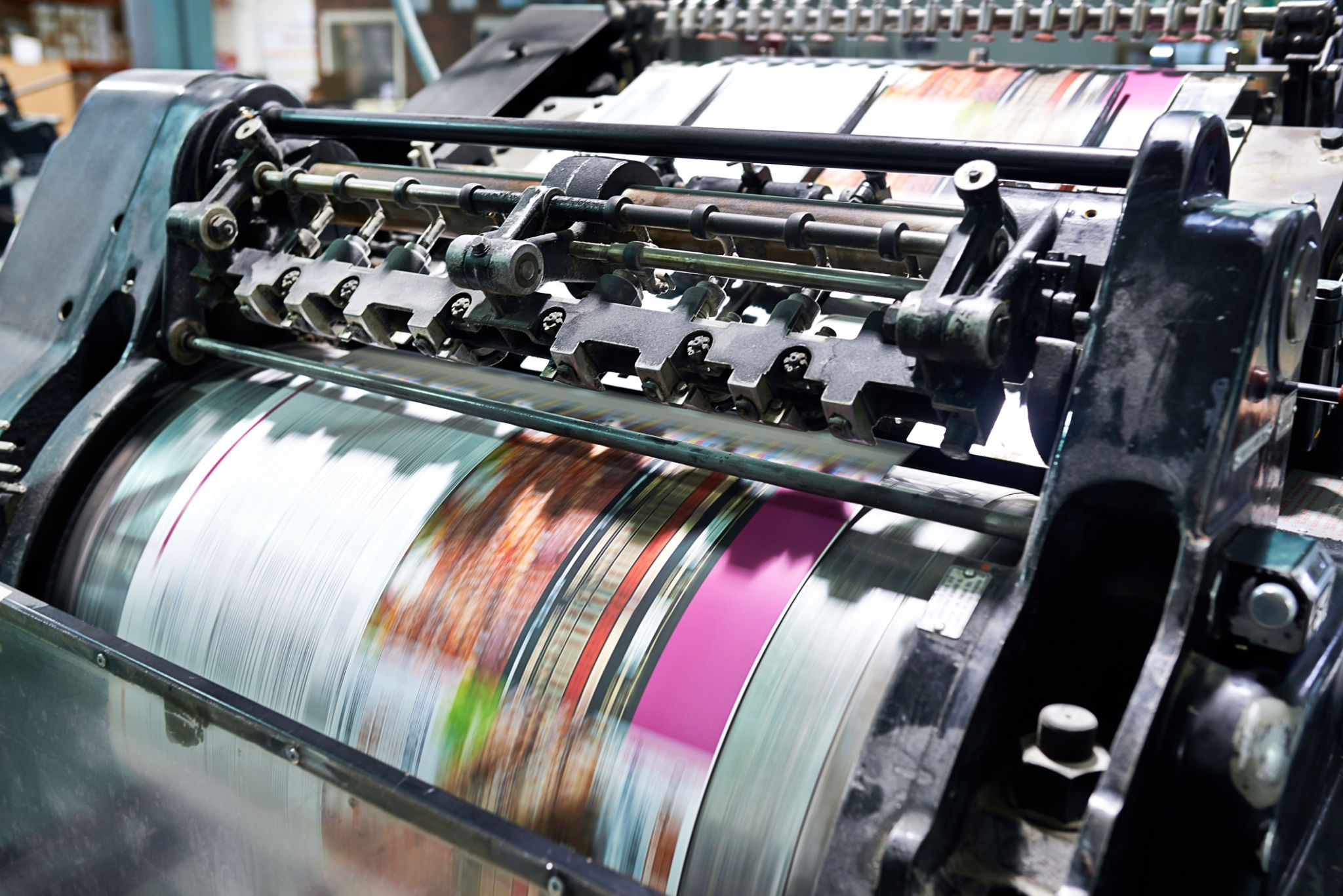
Benefits of Implementing Digital Twins
The integration of digital twins into manufacturing operations brings numerous benefits that are reshaping the industry. Some key advantages include:
- Predictive Maintenance: Digital twins enable predictive maintenance by analyzing real-time data to foresee potential equipment failures and schedule timely interventions.
- Improved Product Design: Manufacturers can utilize digital twins to test and refine product designs before physical prototypes are made, reducing development costs and time.
- Enhanced Quality Control: Continuous monitoring allows for immediate detection of anomalies, ensuring that products meet high-quality standards consistently.
These benefits underscore the importance of digital twins in advancing manufacturing capabilities and maintaining a competitive edge in the market.
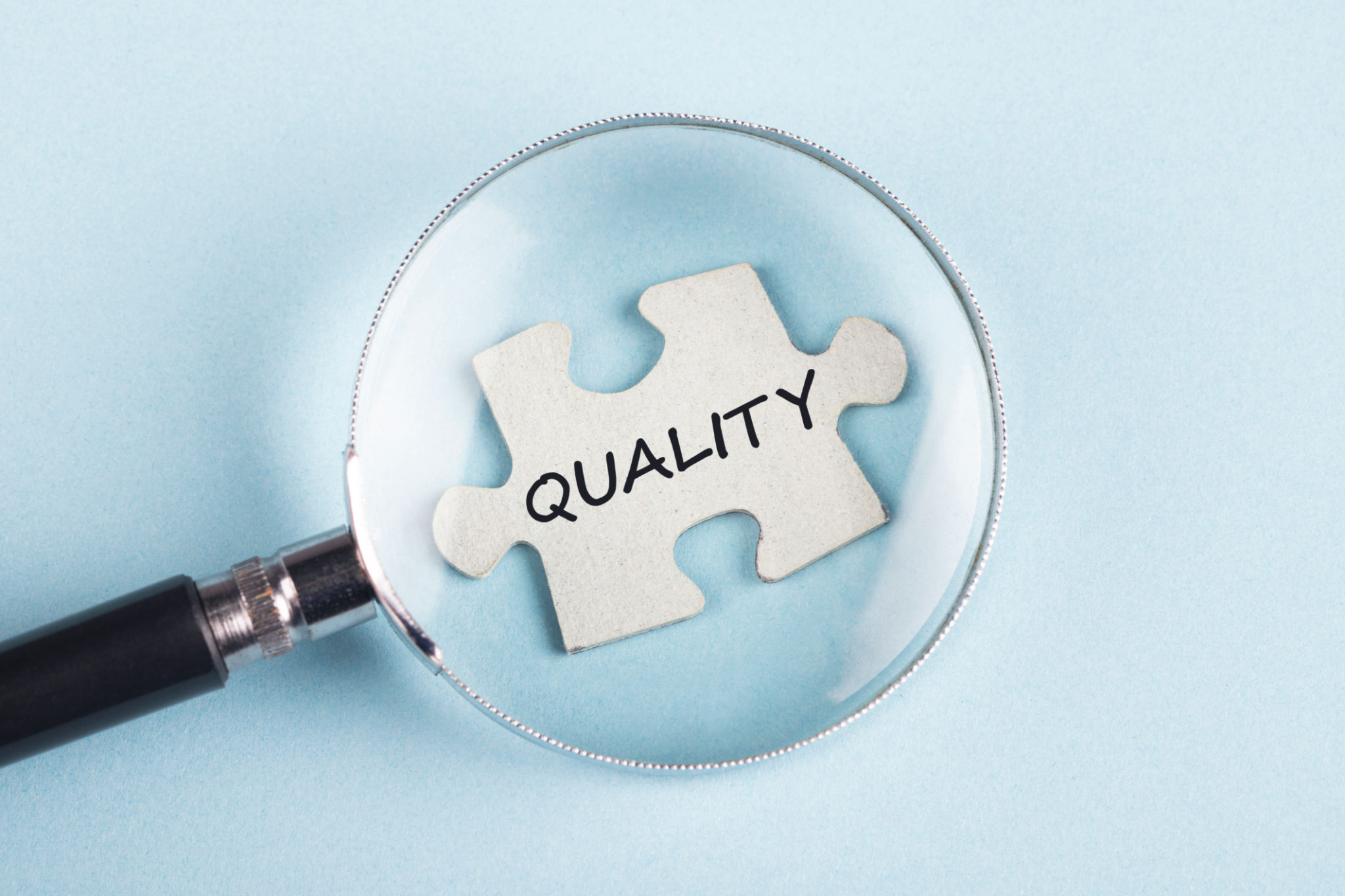
Challenges in Adopting Digital Twins
Despite their numerous advantages, the adoption of digital twins does not come without challenges. One significant hurdle is the integration of legacy systems with new digital twin technologies. Many manufacturers operate with outdated infrastructure that may not be compatible with modern software solutions.
Data security is another concern, as digital twins require extensive data sharing across networks. Ensuring that sensitive information is protected from cyber threats is paramount for successful implementation. Additionally, there is a need for skilled personnel who can manage and interpret complex data generated by digital twins.
The Future of Digital Twins in Industry 4.0
Looking ahead, the future of digital twins in Industry 4.0 appears promising. As technology continues to evolve, we can expect even more sophisticated applications of digital twins that will amplify their impact on manufacturing processes. The integration of artificial intelligence (AI) and the Internet of Things (IoT) will further enhance the capabilities of digital twins, allowing for more autonomous and intelligent operations.
As manufacturers continue to embrace these innovations, digital twins will play an increasingly vital role in driving efficiency, sustainability, and competitiveness in the industry. By leveraging these cutting-edge technologies, companies can look forward to a new era of manufacturing excellence.
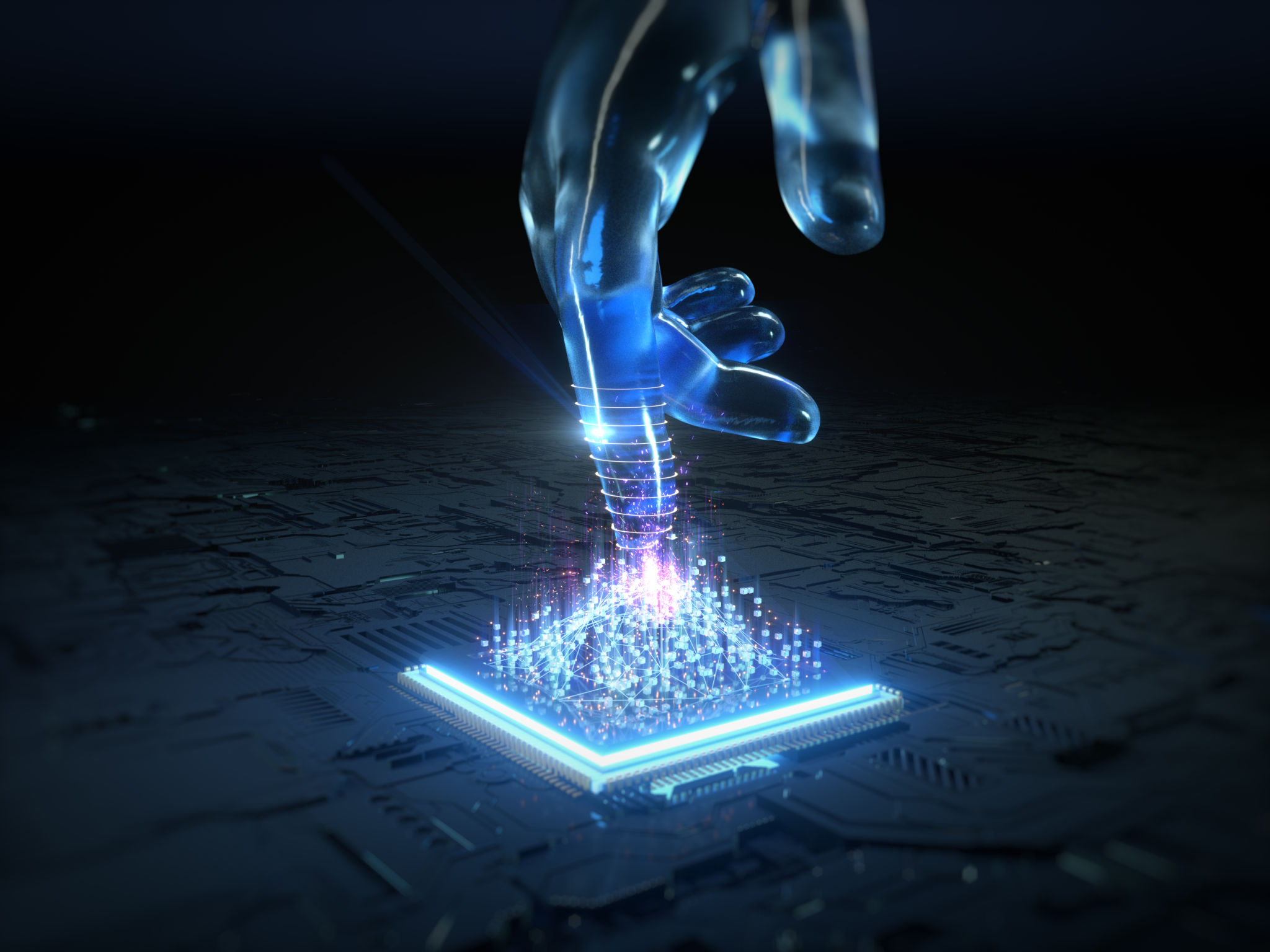